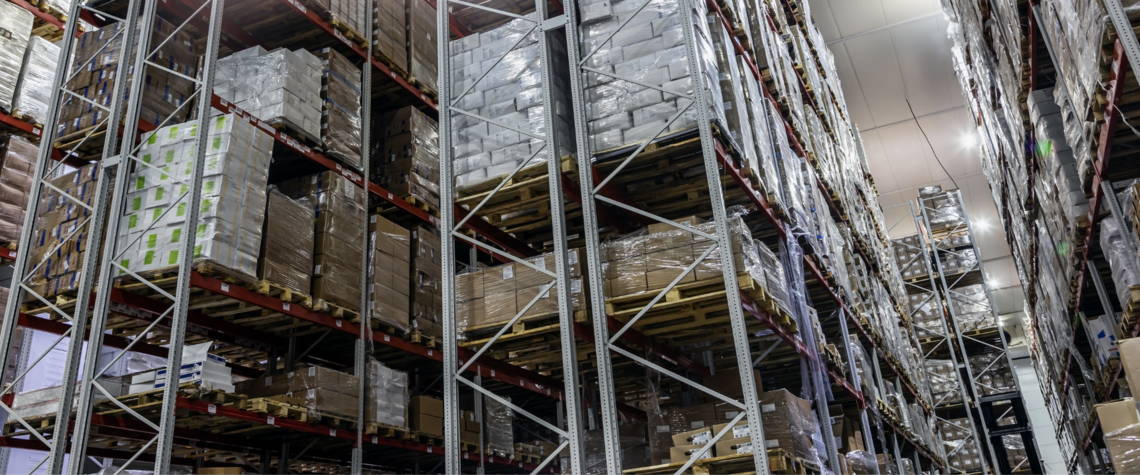
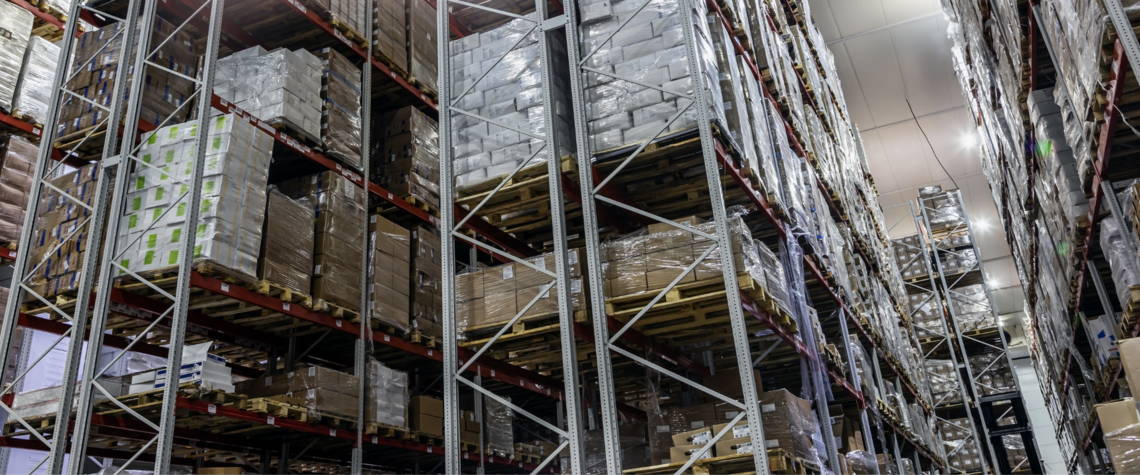
How Cold Storage Advancements Are Transforming Warehouse Operations in Grocery
What was once just a race for speed is now a mad dash for freshness, accuracy, and efficiency. As demand for refrigerated and frozen goods surges, warehouse operators are under pressure to deliver performance in tough conditions, while controlling costs, keeping workers safe, and maintaining strict product standards. In this climate, warehouse automation is no longer a luxury. It’s the foundation for more agile and resilient warehouse operations.
At TGW Logistics, we believe it’s possible to solve cold storage challenges at every stage, from storing temperature-sensitive goods to fulfilling custom pallet orders with pinpoint accuracy. With a bold mix of robotics, AI-driven intelligence, and decades of engineering experience, we’re helping grocery operators thrive, so no matter how hot the competition gets, they can always keep their cool.
Preventing Product Damage and Improving Accuracy
In cold storage, damaged goods are a big liability. Manual forklift operations lead to crushed packaging, temperature fluctuations, and inventory inaccuracies. These issues can increase waste, complicate auditing, and create costly delays downstream. Fully automated systems safely move pallets via conveyors into high-bay storage with a precision that improves inventory transparency and helps account for and protect every product from the moment it enters the warehouse.
The NewCold Burley facility, built in partnership with McCain, is a perfect example of next-generation cold chain automation. Designed to support McCain Foods' nearby processing plant, this $90 million, 180,000-square-foot site features a 138-foot-tall high bay warehouse with 14 rack levels and nearly 90,000 pallet positions. TGW Logistics’ advanced automation, including high-speed conveyors and seven automated stacker cranes, allows the facility to maintain a constant -25°C temperature in the high bay area while streamlining product movement from receiving through dispatch.
By eliminating manual handling and operating as a “dark warehouse” (with no personnel required in the coldest zones), the site improves energy efficiency, reduces labor costs, and protects product integrity, making it a model for what cold storage logistics can achieve at scale.
![[Translate to North America:] cold storage advancements in warehouse operations](/fileadmin/_processed_/d/8/csm_Cold_Storage_Advancements_Blog_Inner_1_45a4cc26b1.png)
![[Translate to North America:] cold storage advancements in warehouse operations](/fileadmin/_processed_/d/8/csm_Cold_Storage_Advancements_Blog_Inner_1_45a4cc26b1.png)
Solving Labor and Ergonomic Challenges with Automation
Few challenges hit grocery logistics harder than labor scarcity. Recruiting, training, and retaining warehouse workers is difficult in any environment, but it’s especially tough in refrigerated and frozen facilities. In traditionally operated cold storage facilities, the physical toll on workers is significant. Employees must wear heavy protective gear, which limits dexterity, slows movement, and contributes to fatigue. Tasks like lifting, bending, and stacking cases in sub-zero temperatures are inefficient and increase the risk of injury and high turnover.
Automation directly addresses these challenges. Robotic systems and ergonomic workstations reduce strain, improve safety, and allow workers to operate more comfortably and efficiently. TGW Logistics’ FullPick system helps take that further by automating heavy and repetitive tasks like case picking and pallet building. Instead of manually stacking cases in harsh conditions, workers oversee intelligent systems that handle the load with precision and consistency. By removing physical limitations and reducing labor exposure to freezing environments, warehouse automation creates safer, more sustainable jobs and enables operations to run faster, longer, and with fewer disruptions.
Store-Ready Pallets That Improve Delivery Efficiency
It’s important to preserve the product while preparing it for fast, accurate delivery. In manual environments, picking is often done with little regard for store layout or delivery route, which leads to disorganized pallets, longer unloading times, and buried products that require digging and reshuffling. Our software solves that by sequencing cases based on the destination. Whether it’s a grocery aisle, a gas station, or a school cafeteria, pallets are built to match the layout of the receiving location for fewer touches, faster restocks, and dramatically reduced delivery time.
These benefits apply across the food service spectrum, touching grocery chains, convenience stores, and institutional kitchens. For example, TGW Logistics systems can build a pallet organized for a specific grocery aisle, allowing shelf stockers to wheel it straight to its destination and unload efficiently. For a gas station, the pallet is built to match the store's layout, so the delivery driver can quickly drop off what’s needed without digging through mixed freight. Such precision reduces delivery time, lowers strain on drivers, and helps shorten the overall route, resulting in fewer trailers needed, fewer stops per day, and meaningful cost savings. In a business where margins are razor-thin, that kind of operational efficiency can make all the difference.
Why Warehouse Automation Works So Well in Cold Chain Environments
What makes warehouse automation especially powerful in cold chain environments is its ability to consistently perform in conditions that challenge human workers.
Automated storage and retrieval systems (AS/RS) bring major benefits to cold storage warehouse operations:
- Reduce energy use through compact facility layouts and dark storage zones
- Lower spoilage and shrinkage by improving inventory rotation and expiration tracking
- Streamline operations with software-driven intelligence across picking, storage, and shipping
- Adapt faster to seasonal surges or last-minute changes without overburdening the team
- Scale more easily without the complexities of adding and training new labor
- Minimize injury risk, improve workplace safety, and reduce lost-time incidents
Automation also introduces consistency, removing variables caused by shift changes, staff shortages, or training gaps. By standardizing core warehouse processes, grocers can deliver a more reliable customer experience and build a more predictable business model. That’s a competitive edge in an industry where even minor disruptions can have major consequences.
Dig deeper into TGW Logistics’ Guide to Warehouse Automation to see how robotic shuttle systems, compact footprints, and intelligent software combine to create high-efficiency environments with lower energy consumption, making them ideal for cold storage.
![[Translate to North America:] cold storage advancements warehouse operations](/fileadmin/_processed_/a/2/csm_Cold_Storage_Advancements_Blog_Inner__2_79c26b8813.png)
![[Translate to North America:] cold storage advancements warehouse operations](/fileadmin/_processed_/a/2/csm_Cold_Storage_Advancements_Blog_Inner__2_79c26b8813.png)
Cold Chain Automation Is Going Green
While automation’s operational benefits are clear, there is also a growing concern about its environmental impact.
Energy efficiency is a core consideration in refrigerated warehouses, and automation helps cut consumption through:
- More compact facility designs
- Reduced waste due to damage or spoilage
- Streamlined inventory movement that prevents overcooling
Cold storage automation also reduces food waste through better inventory rotation and expiration-aware picking strategies. By intelligently prioritizing soon-to-expire goods for earlier delivery, automated systems minimize product loss and help grocers meet sustainability targets.
These are major drivers behind the projected growth of the cold chain automation market, which is expected to surpass $2 billion in revenue by 2030, according to a recent analysis by Modern Materials Handling. With pressure mounting for grocers to meet ESG goals, automated solutions can be part of a broader plan.
The Future of Cold Chain Logistics Is Already Here
We build today’s systems, but more importantly, we’re preparing for tomorrow’s. Advanced technologies, like digital twins, are helping warehouse operators visualize performance in real-time, supporting predictive maintenance and continuous improvement. Robotics are becoming more adaptable, working end-to-end across receiving, storage, picking, and shipping.
Even the art of palletizing is evolving. TGW Logistics’ background software “thinks” strategically, arranging pallets in the most efficient way possible based on store needs, product fragility, and delivery routes. And while blockchain isn’t yet fully integrated, it’s on the horizon. Since food safety and supply chain transparency are non-negotiable, blockchain-enabled cold chains could offer unparalleled traceability from farm to shelf.
Rethinking Cold Storage Warehouse Operations from the Inside Out
Cold storage success starts with reconsidering how your warehouse operations function, from labor and ergonomics to inventory accuracy and delivery precision. Manual processes are no match for the market’s complexity, and grocers can’t afford inefficiency in facilities that operate 24/7. At TGW Logistics, we believe automation makes it possible to reduce labor strain, cut costs, prevent damage, and improve efficiency across the board. Whether you're building store-ready pallets or scaling up for peak season, our solutions help you stay competitive in a cold environment that’s only getting hotter.
With intelligent systems like FullPick, software-driven pallet sequencing, and dark warehouse designs, we’re helping grocery warehouse operations thrive under pressure, transforming pain points into performance drivers with practical, proven progress that helps grocers deliver on freshness, speed, and profitability. Let’s build a cold storage operation that works smarter—inside and out. Contact us today to learn more.