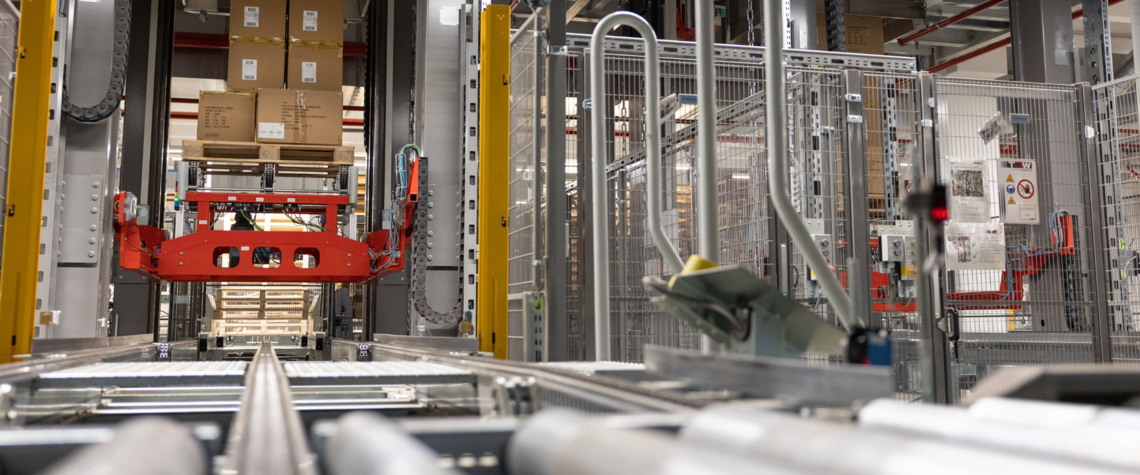
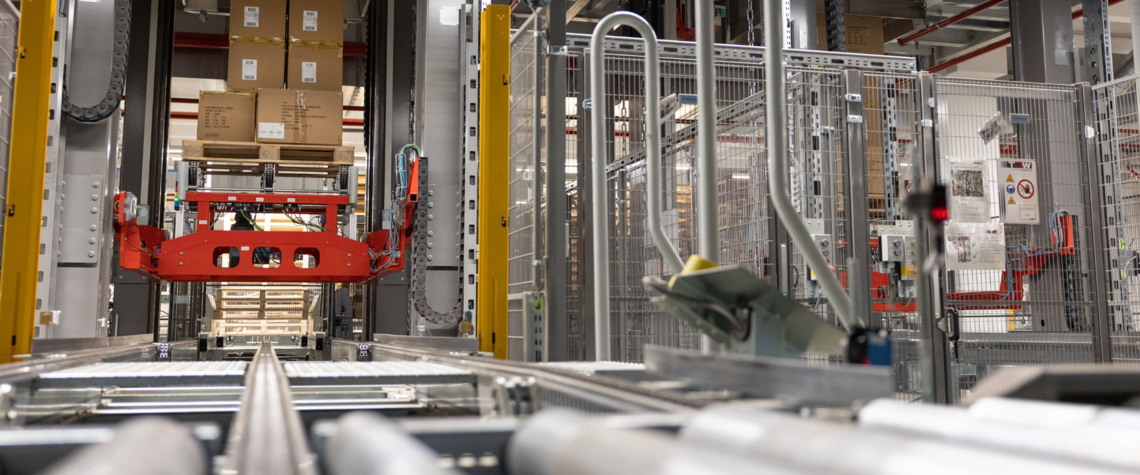
Real-World Application in Automotive Logistics
Manufacturers face unprecedented pressure to deliver components exactly when needed in high-throughput manufacturing environments. Material handling systems must overcome significant challenges: maintaining optimal inventory levels, minimizing floor space utilization, and reducing labor dependencies while meeting increasingly demanding production schedules. The critical process of line replenishment sits at the center of this challenge, where even the slightest delays can cascade into costly production interruptions.
Manufacturers seeking to optimize their replenishment processes now turn to automated storage and retrieval system (ASRS) solutions as transformative technologies and mobile robotics. These advanced systems don't just store components; they deliver them precisely when and where production needs them, creating a synchronized flow that keeps production lines running smoothly even as demand fluctuates.
The Role of Line and Kanban Replenishment in Lean Manufacturing
Kanban systems represent the beating heart of lean manufacturing environments. Originally developed as part of Toyota's production system, Kanban uses visual signals to trigger the movement of materials only when needed, creating a pull-based approach that minimizes waste and maximizes efficiency.
Line replenishment is a strategic imperative in effective lean manufacturing, not merely a logistics function. Timely component delivery directly supports uninterrupted production, preventing the costly stops and starts that plague less efficient operations. Kanban workflows establish standardized processes that ensure consistency, moving each component through the system based on actual consumption rather than forecasted demand.
This methodology aligns perfectly with Just-in-Time (JIT) principles, which aim to deliver the correct parts, in the correct quantity, at the correct location, exactly when needed. Correctly implemented Kanban replenishment creates a synchronized rhythm throughout the production environment, delivering each component precisely as workers finish with the previous one.
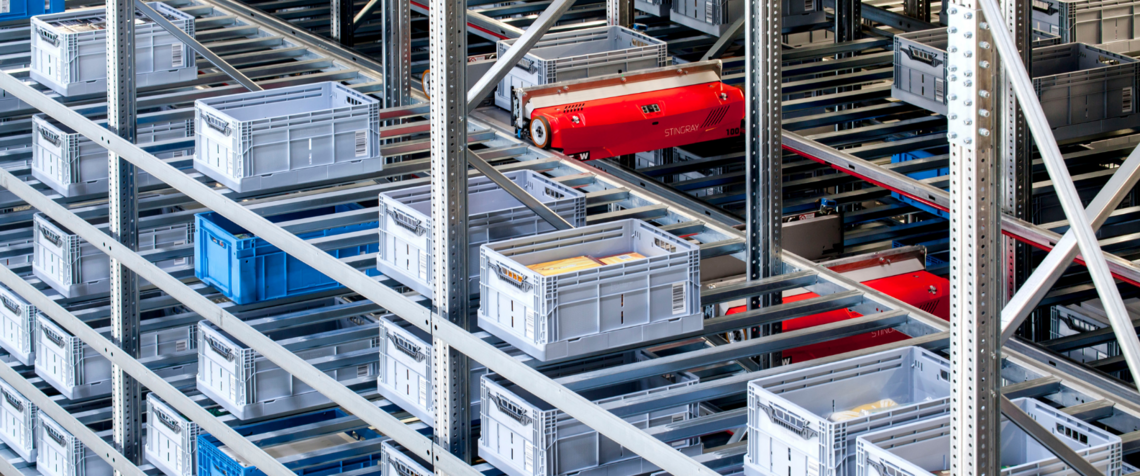
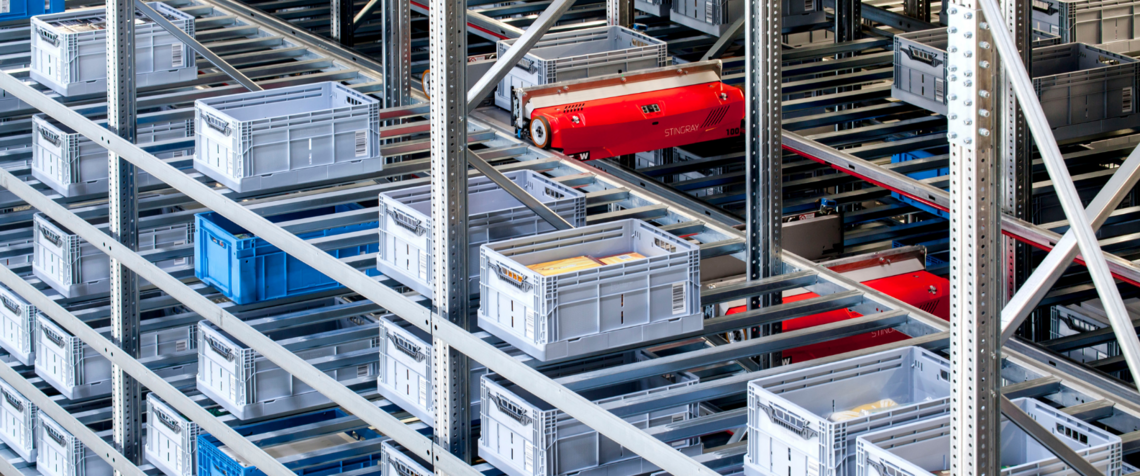
Where Manual Replenishment Falls Short
While Kanban principles are sound, their execution through manual systems often introduces significant inefficiencies. Manual replenishment processes typically suffer from several critical limitations:
- Inconsistent timing: Human-driven replenishment creates variable delivery times, making it difficult to maintain the precise scheduling needed for JIT production.
- Error-prone processes: Manual picking and delivering components introduces the potential for selection errors, quantity mistakes, and misplaced materials.
- Labor dependencies: Traditional replenishment relies heavily on manual labor, making systems vulnerable to staffing shortages and turnover issues.
- Limited visibility: Without automated tracking, inventory accuracy suffers, leading to either overstocking (wasting space and capital) or stockouts (halting production).
- Safety concerns: Manual material handling increases injury risks, particularly in environments with heavy components or high-frequency movements.
These manual limitations become increasingly pronounced as production environments grow more complex with expanding SKU counts and variable batch sizes. These limitations create replenishment systems that struggle to keep pace with modern manufacturing demands, causing bottlenecks that constrain overall throughput.
How An Automated Storage and Retrieval System Optimizes Replenishment
Automated storage and retrieval system technology, especially when integrated with mobile robotics, fundamentally reimagines replenishment by creating a demand-driven, real-time flow of materials. These systems deliver components precisely when needed, maintaining the Kanban principle of pull-based movement while eliminating manual handling inefficiencies.
The core benefits of automated storage and retrieval system technology for line replenishment include:
- Demand-driven delivery: Components are automatically retrieved and delivered based on production requirements, creating a truly responsive system.
- Space optimization: Vertical storage utilization can reduce floor space requirements by up to 85% compared to conventional shelving, placing more inventory closer to the point of use.
- Increased accuracy: Automated systems achieve up to 99.9% picking accuracy, virtually eliminating errors that disrupt production.
- Reduced labor dependency: Automation handles routine retrieval and transport tasks, allowing staff to focus on higher-value activities.
- Enhanced visibility: Components can be easily transported to and from production lines via conveyor or Mobile Robotics, creating efficient material flow throughout the facility.
TGW Logistics seamlessly integrates automated storage and retrieval systems with SAFELOG mobile robots, combining high-density storage with flexible, scalable movement of goods. This approach ensures not only precise storage and retrieval, but also dynamic, efficient transportation of all item types—tailored to your unique facility layout and flow.
TGW Logistics’ Approach to Replenishment Automation
At TGW Logistics, we recognize that effective replenishment automation requires more than technology—it demands a deep understanding of your unique production workflow. We begin our approach with a comprehensive analysis of your specific challenges, designing solutions that integrate seamlessly with your existing processes while delivering transformative improvements.
Our replenishment automation solutions are built around three core principles:
We design systems that adapt to your evolving needs, allowing you to expand capacity or modify workflows as your production requirements change. This flexibility ensures that your automation investment continues to deliver value even as your business evolves.
With decades of experience in industrial logistics and automotive logistics, we develop solutions specifically engineered for high-throughput manufacturing environments. This specialized focus ensures that our systems address the unique challenges of production-oriented material handling.
Rather than forcing your operation to conform to predefined systems, we tailor our solutions to your specific needs, creating a custom approach that optimizes your production environment.
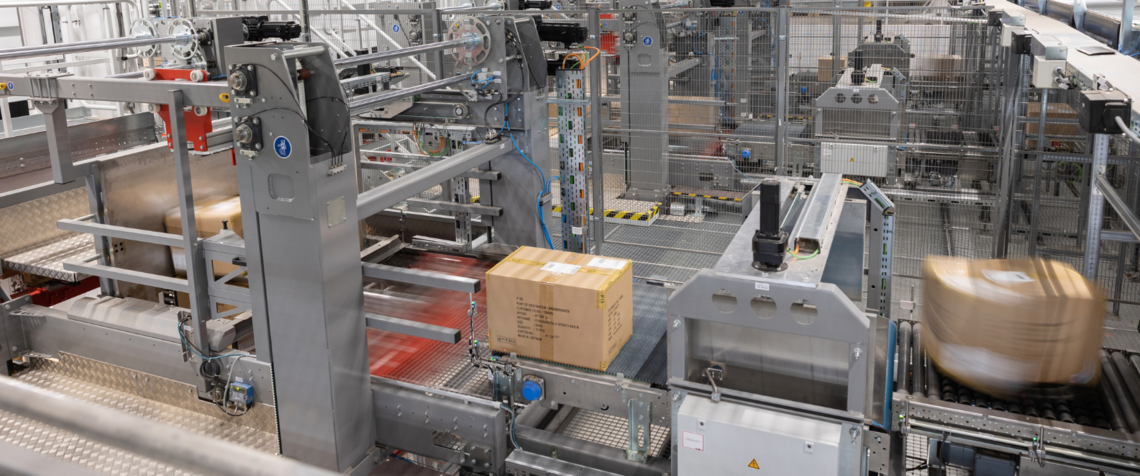
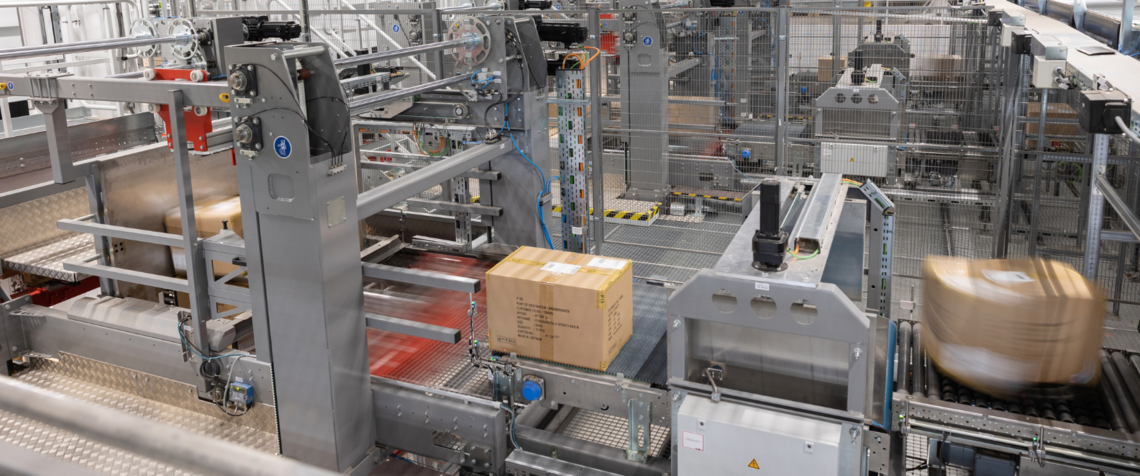
Real-World Application in Automotive Logistics
The automotive sector presents some of the most challenging replenishment scenarios, with thousands of components requiring precise delivery across complex production lines. Implementing ASRS for Kanban replenishment has delivered dramatic results.
For example, RECA Kellner & Kunz implemented a TGW Logistics ASRS solution to support Kanban-driven replenishment, enabling precise, real-time delivery of components across their production process.
For many of our automotive customers, implementing ASRS transformed their operations through:
- Synchronized delivery: Components arrive at assembly stations in perfect sequence, eliminating delays and reducing line-side inventory requirements.
- Compact buffer storage: Vertical storage systems manage high-density inventory, keeping more components close to the production line without consuming valuable floor space.
- Error reduction: Automated picking eliminates incorrect part delivery, reducing rework and quality issues.
- Enhanced responsiveness: Real-time inventory visibility enables immediate adaptation to production schedule changes, supporting flexible manufacturing.
Through these improvements, automotive manufacturers achieve measurable gains in production efficiency, increasing throughput, reducing downtime, and saving significant costs in labor and inventory management.
At Bileko Car Parts, implementing TGW Logistics’ shuttle system enabled fast, automated spare parts fulfillment, supporting over 40,000 active SKUs and ensuring next-day delivery throughout Sweden.
WMS, WCS, and Automated Storage and Retrieval in Harmony
The full potential of ASRS technology for line replenishment comes through seamless integration with warehouse management systems (WMS) and warehouse control systems (WCS). This technological ecosystem creates a coordinated flow from order to delivery, with each system playing a specific role:
Provides overall inventory management, tracking stock levels and locations while planning replenishment based on production requirements.
Coordinates the movement of materials through automation systems, optimizing routes and prioritizing urgent replenishment needs.
Functions as a comprehensive control system that combines WMS and WCS capabilities while delivering additional key feature, including Analytics, Material Flow Control (MFC), SAV (Shuttle Application Visualization), carrier management, and more. Enhances control and system responsiveness, ensuring the entire ecosystem functions as a cohesive unit.
This integrated approach aligns replenishment precisely with actual production demand, using real-time communication between systems to create a dynamic flow that adapts to changing priorities and requirements.
Faster Throughput, Lower Costs, Fewer Errors
The implementation of ASRS for line and Kanban replenishment delivers measurable benefits across multiple dimensions:
- Production continuity: The steady, reliable flow of materials results in significantly fewer line stoppages, maximizing productive uptime.
- Labor optimization: Automation reduces direct labor costs while allowing staff to focus on value-adding activities rather than routine transport tasks.
- Inventory precision: Enhanced accuracy in stock levels and component location simplifies management while reducing safety stock requirements.
- Throughput gains: Consistent delivery timing increases production capacity by eliminating delays in replenishment.
These benefits together create a compelling return on investment, with most systems achieving payback within 3-5 years while delivering ongoing operational advantages.
Future-Ready Production
Most importantly, automated replenishment creates a foundation for ongoing growth and adaptation. TGW Logistics' systems provide the flexibility to accommodate changing needs as your production requirements evolve:
- SKU expansion: Systems quickly adapt to handle growing component varieties without compromising efficiency.
- Volume scaling: Modular design increases throughput capacity as production volumes grow.
- Facility evolution: Solutions work effectively in both brownfield retrofits and greenfield implementations, supporting your long-term facility strategy.
- Digital transformation: Advanced integration capabilities support broader smart factory initiatives, positioning your operation for future innovation.
It's Possible With TGW Logistics
Optimizing your line and Kanban replenishment offers more than operational improvement—it provides a strategic advantage in today's competitive manufacturing environment. TGW Logistics' automated storage and retrieval system solutions transform your replenishment process from a potential constraint into a powerful enabler of production excellence.
Discover how we can help you reduce labor costs, improve delivery accuracy, and scale your warehouse production with flexible, modular solutions. Contact TGW Logistics today to start planning your automation strategy and experience the difference that optimized replenishment can make in your operation.
TGW Logistics is a foundation-owned company headquartered in Austria and a global leader in warehouse automation and warehouse logistics. As a trusted systems integrator with more than 50 years of experience, we deliver end-to-end services: designing, implementing, and maintaining fulfillment centers powered by mechatronics, robotics, and advanced software solutions. With over 4,500 employees spanning Europe, Asia, and North America, we combine expertise, innovation, and a customer-centric dedication to help keep your business growing. With TGW Logistics, it's possible to transform your warehouse logistics into a competitive advantage.