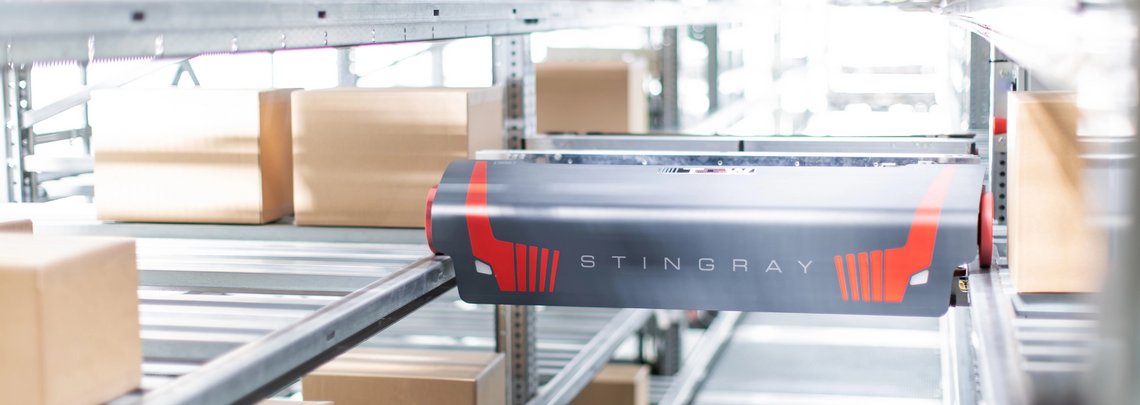
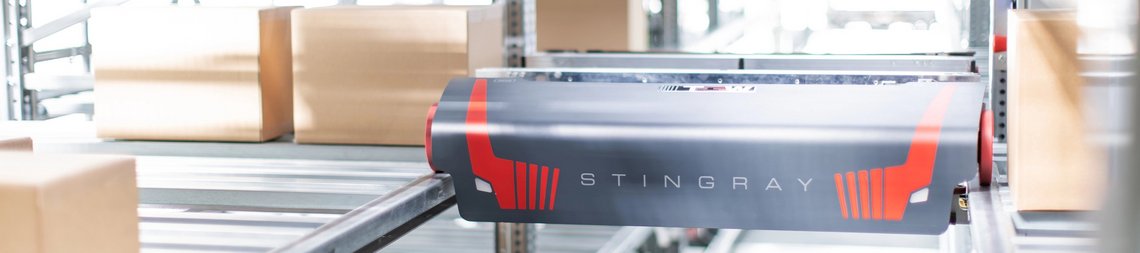
TGW Logistics
News, Events & Resources
TGW Logistics is a foundation-owned company headquartered in Austria and a global leader in warehouse automation and warehouse logistics. As a trusted systems integrator with more than 50 years of experience, we deliver end-to-end services: designing, implementing, and maintaining fulfillment centers powered by mechatronics, robotics, and advanced software solutions. With over 4,500 employees spanning Europe, Asia, and North America, we combine expertise, innovation, and a customer-centric dedication to help keep your business growing. With TGW Logistics, it's possible to transform your warehouse logistics into a competitive advantage.