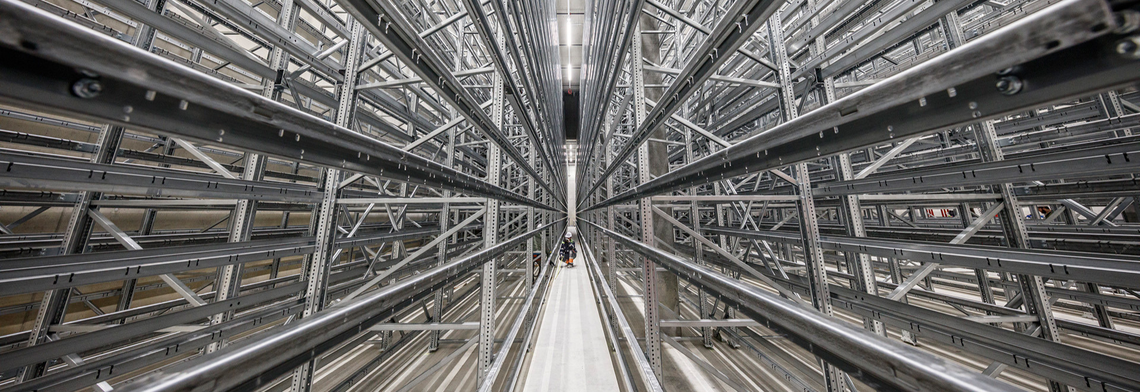
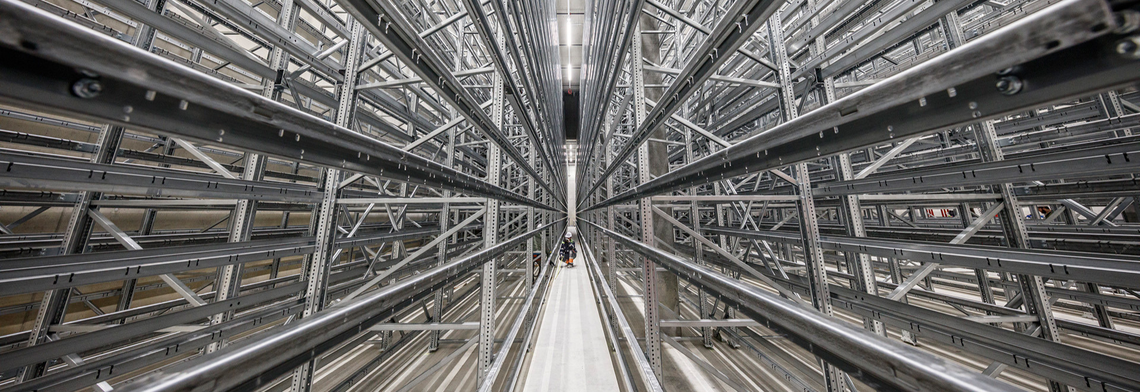
TGW Logistics Makes It Possible
Customer Success Stories
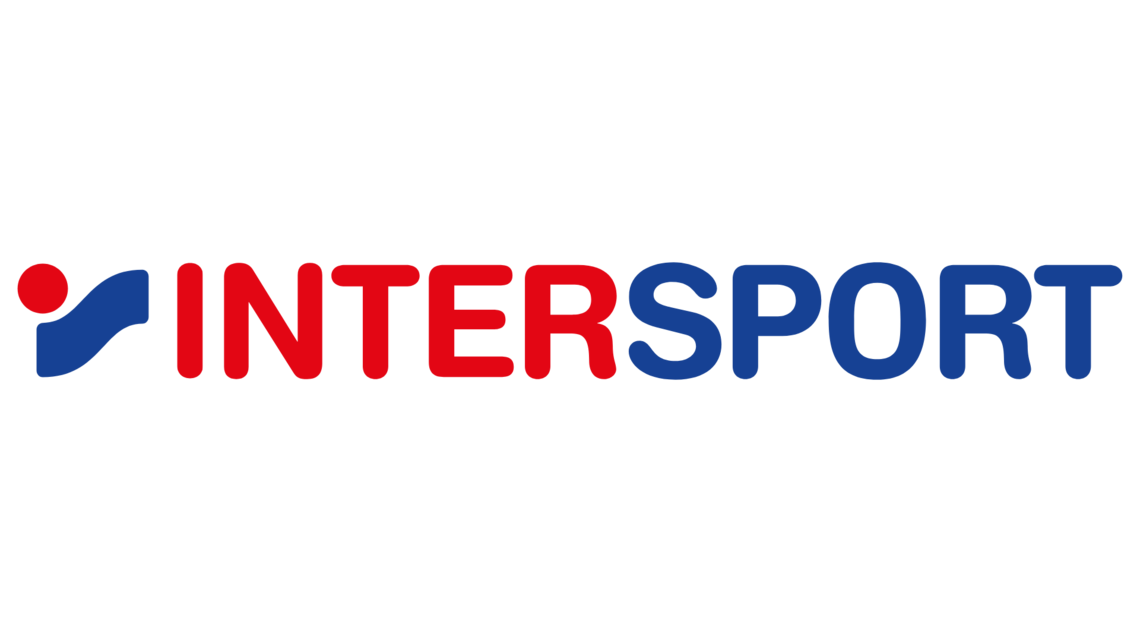
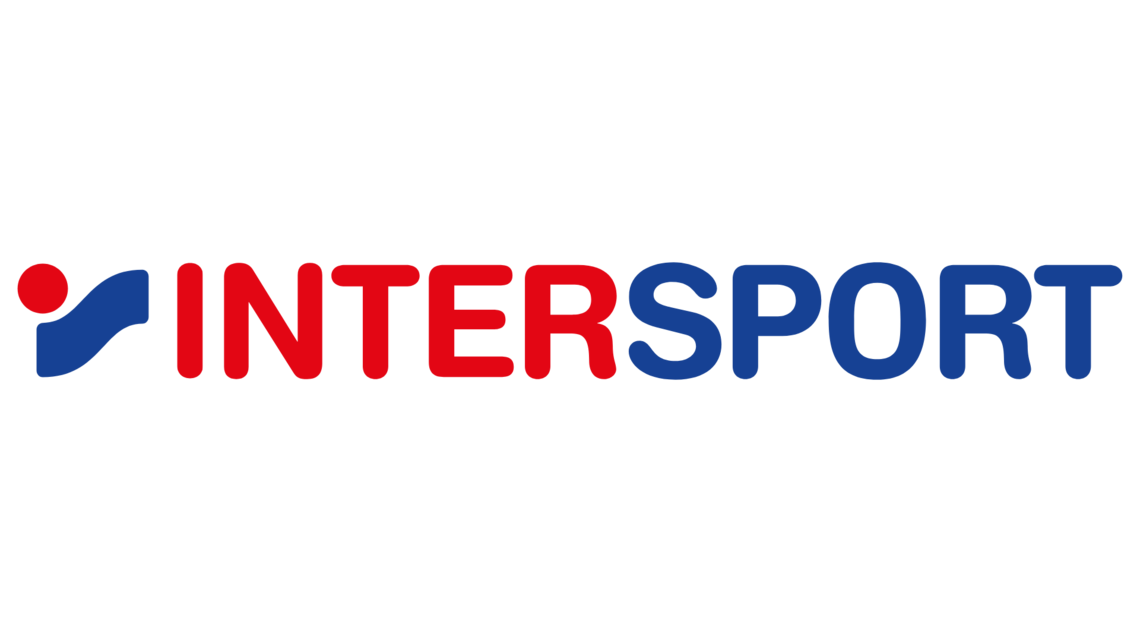
Consumer Goods
INTERSPORT: A milestone in the company's history
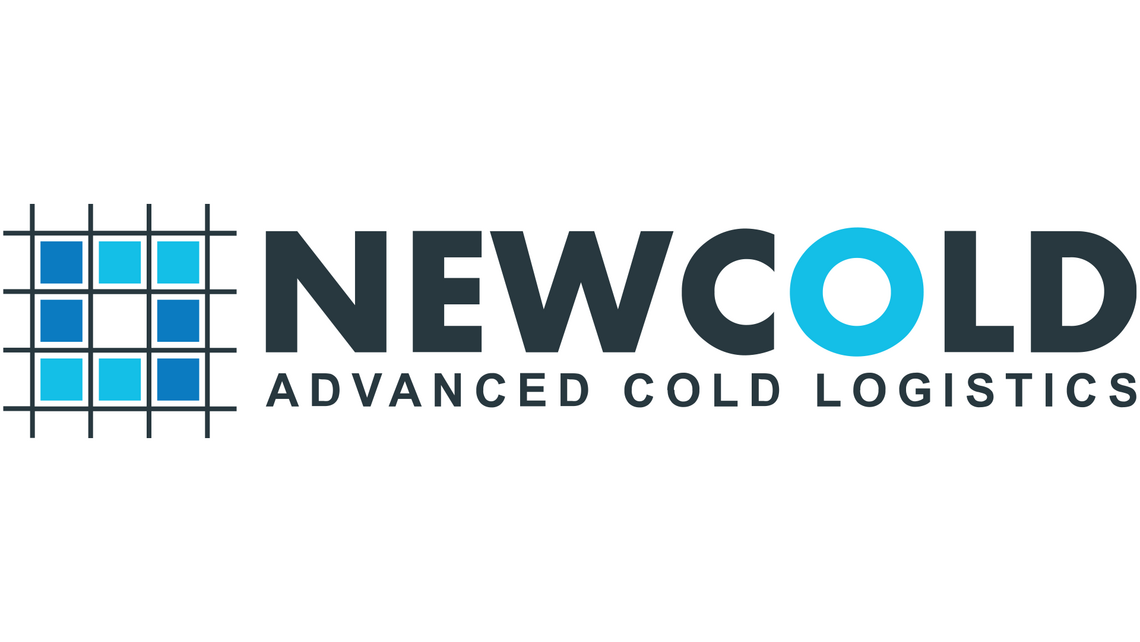
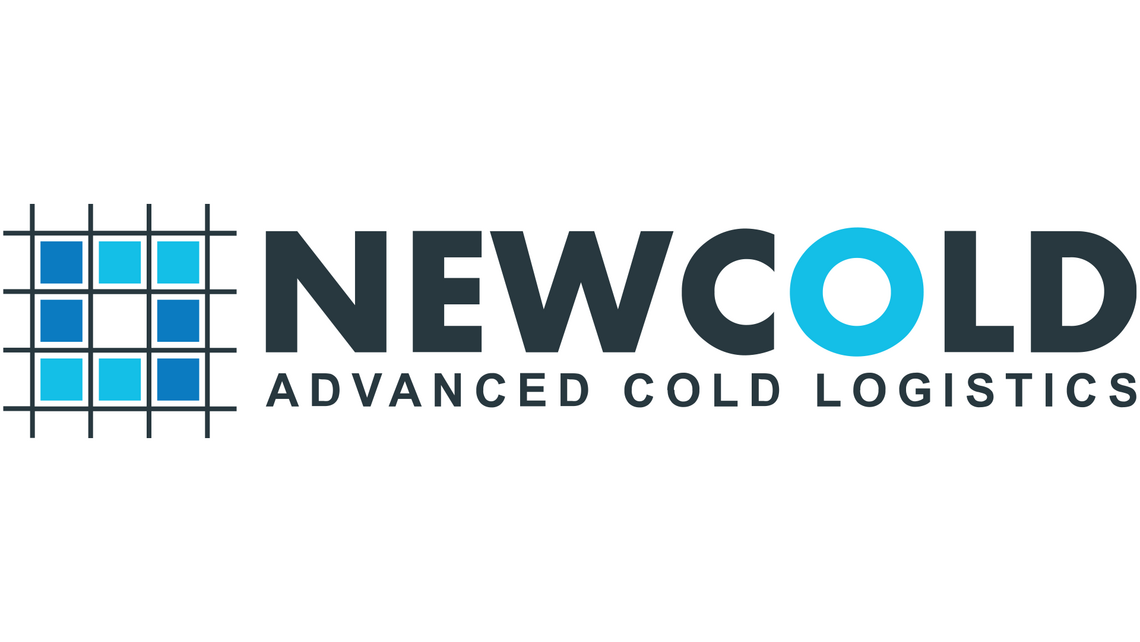
Grocery
Grocery Retail
Automated Performance at -25°C for NewCold and McCain Foods
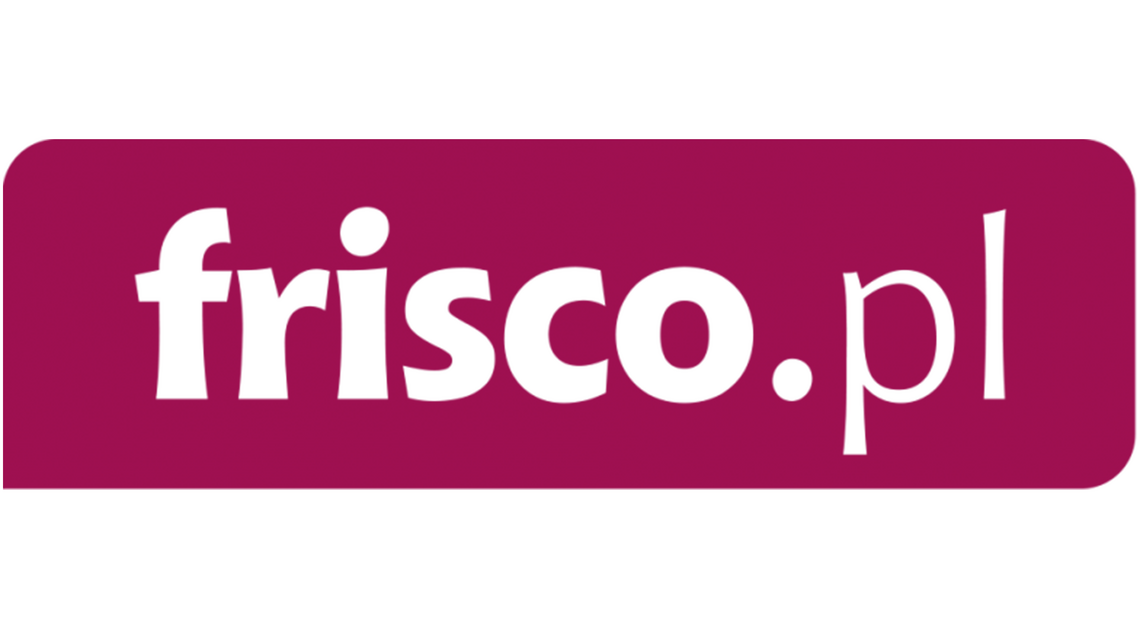
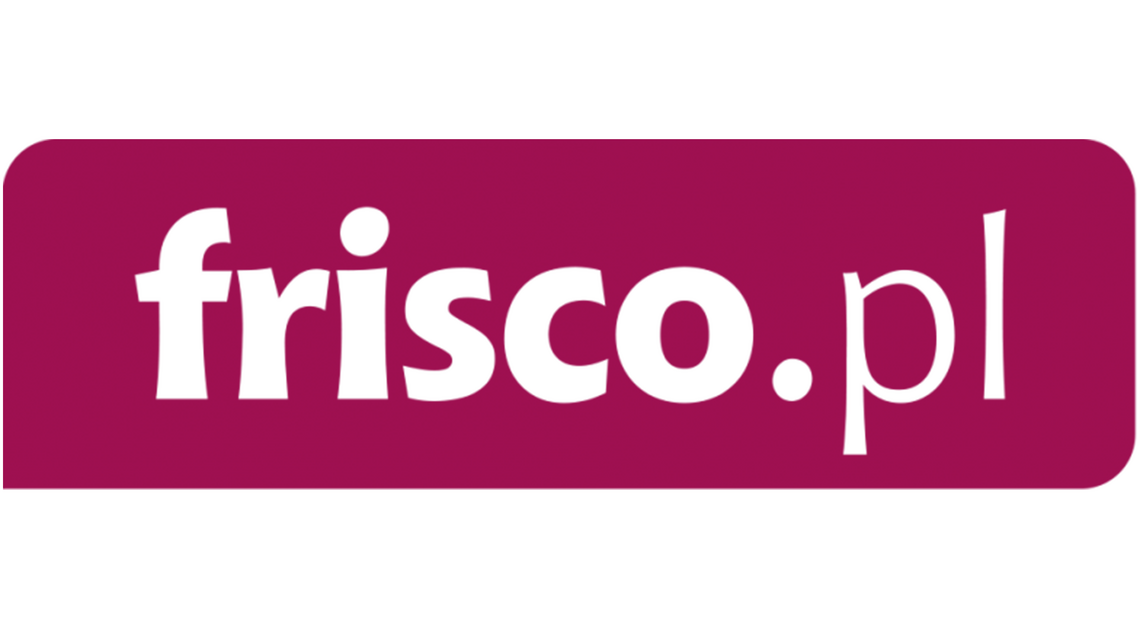
Grocery
Grocery Retail
How Automated Picking Quadrupled Frisco’s Order Capacity
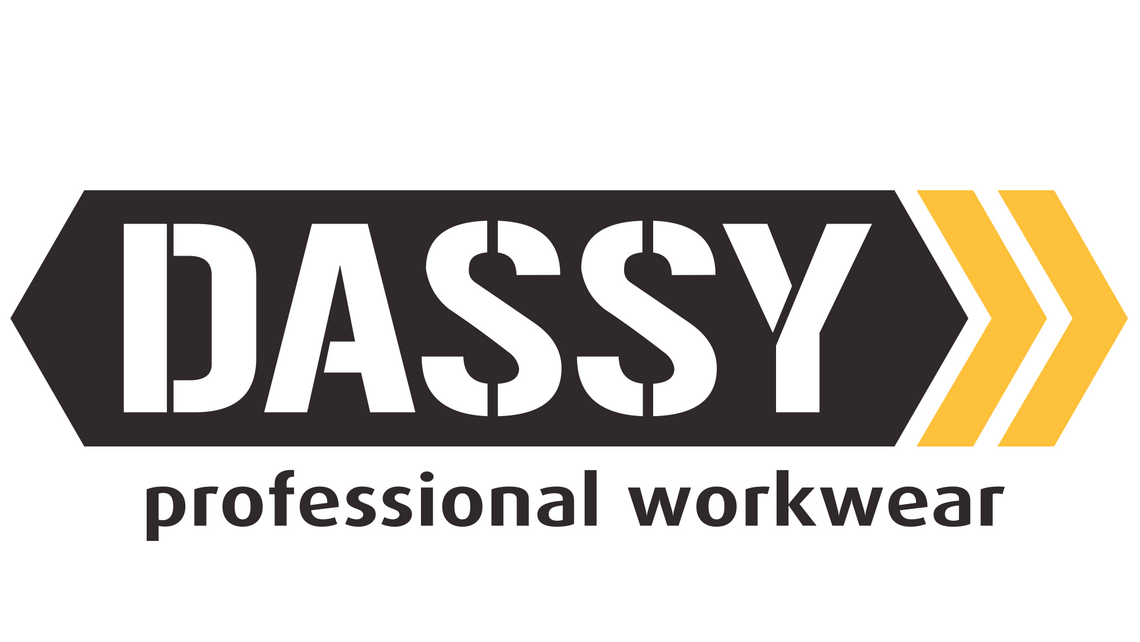
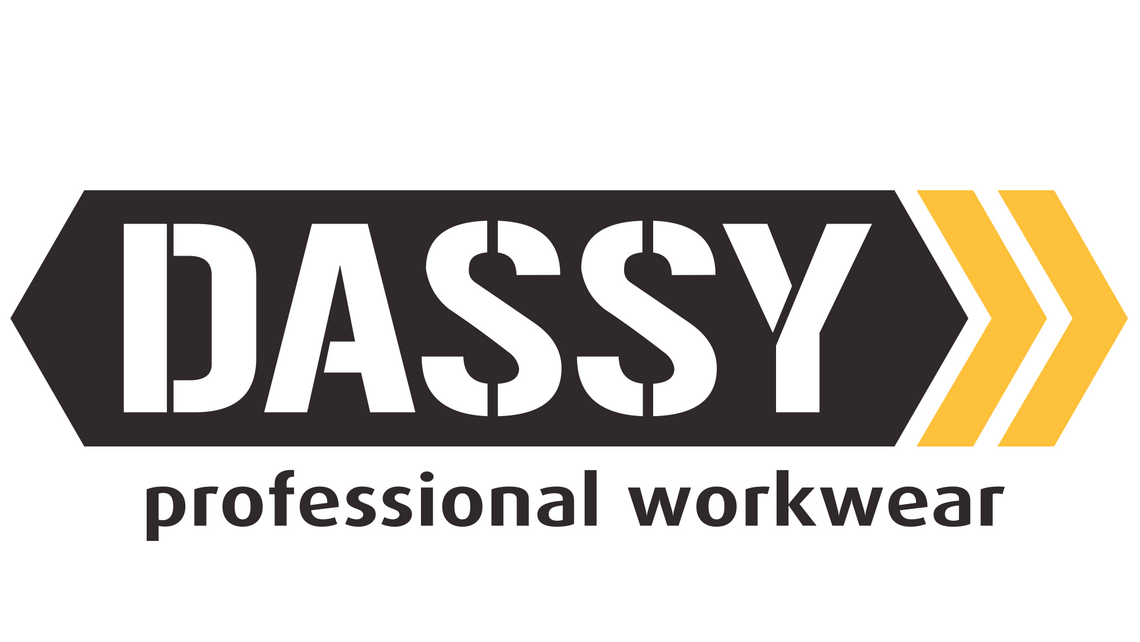
Fashion & Apparel
Boosted Productivity, Storage and Flexibility for Dassy
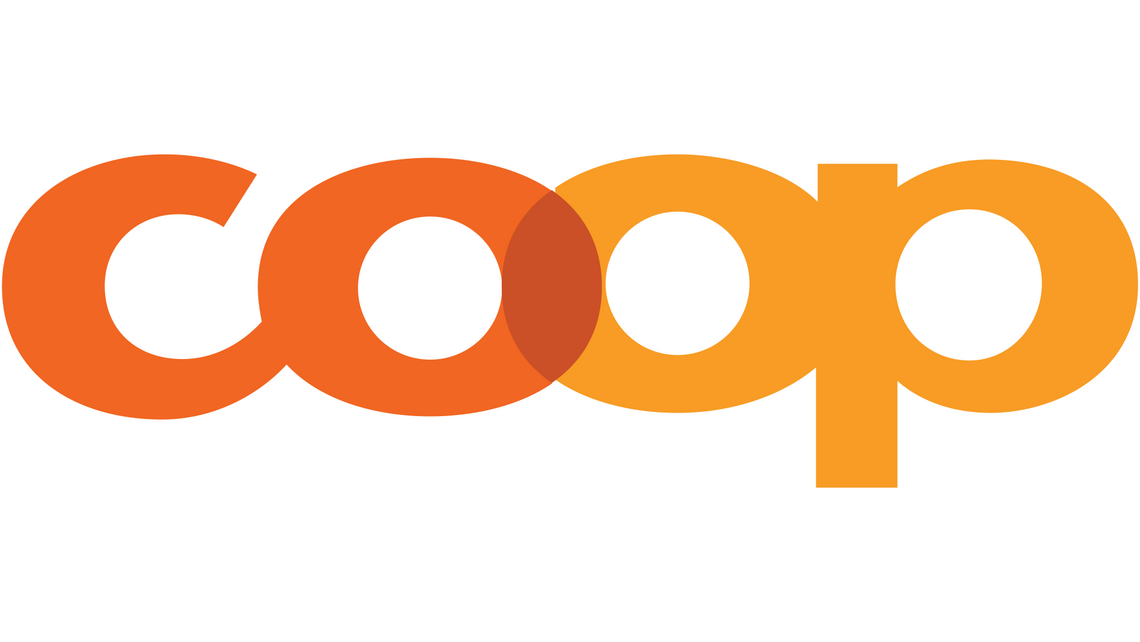
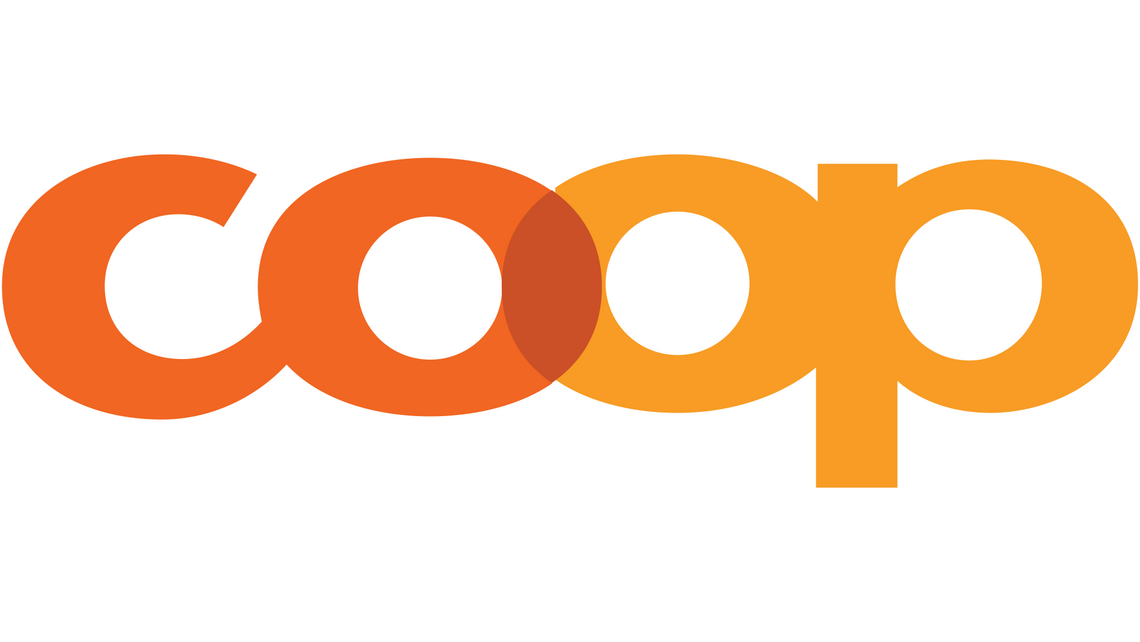
Grocery
Grocery Retail
Improved Energy Efficiency in Cold Chain Logistics for Coop
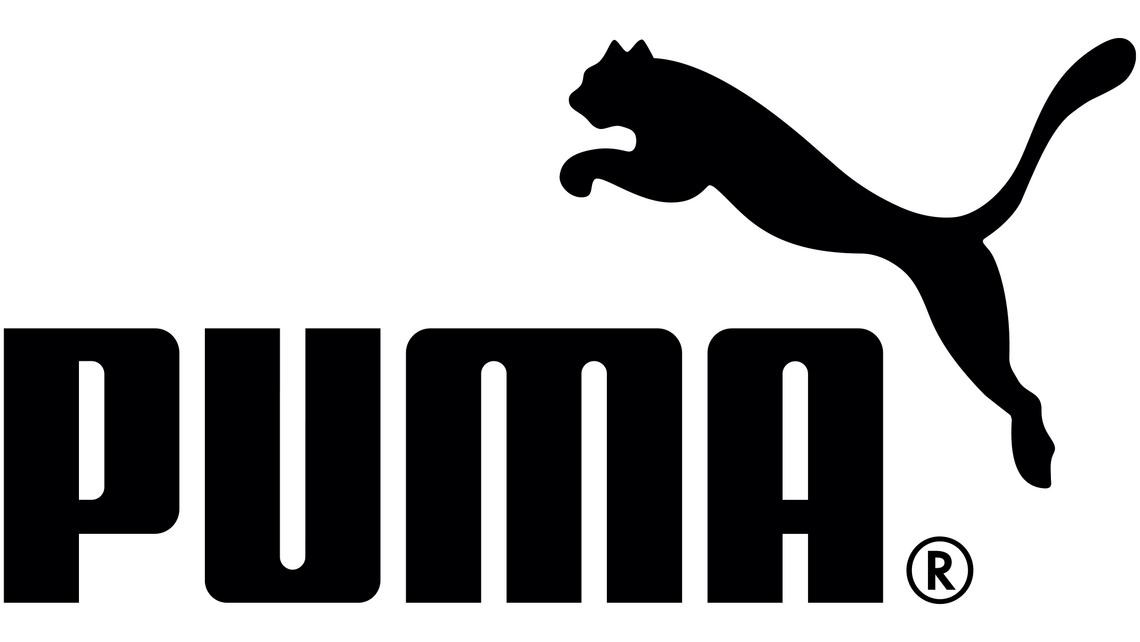
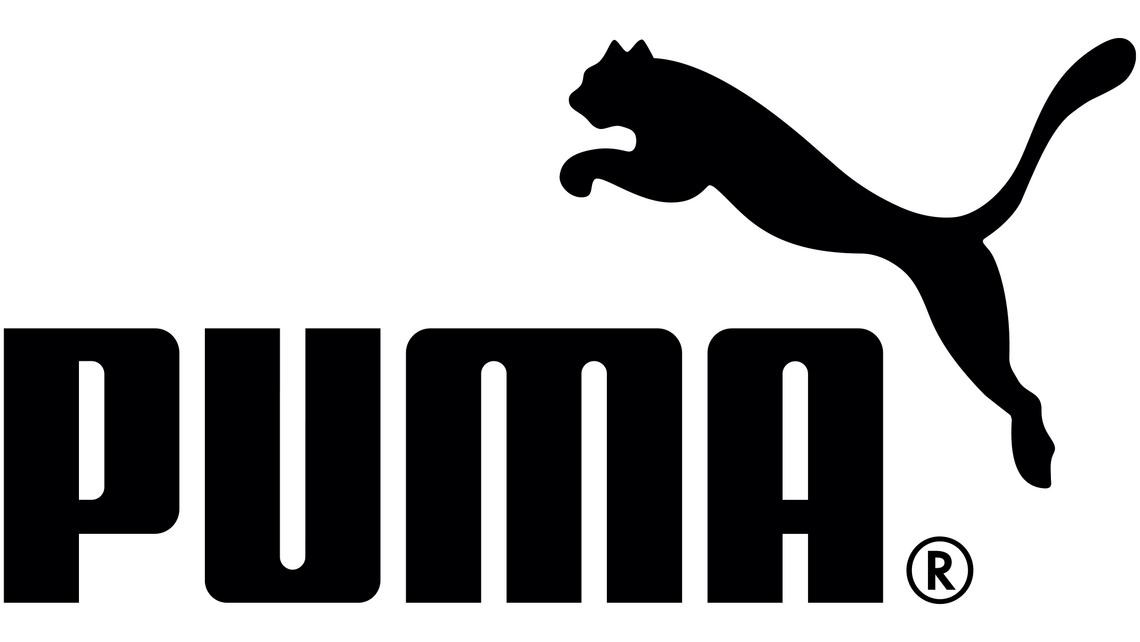
Fashion & Apparel
Puma Makes Omni Channel Logistics a Reality
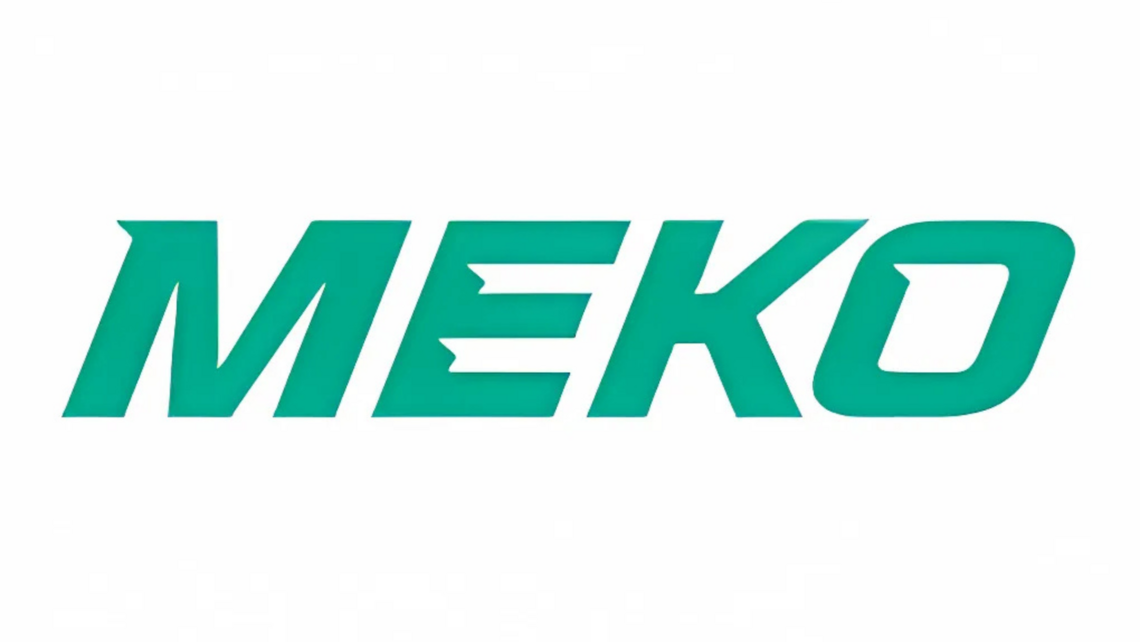
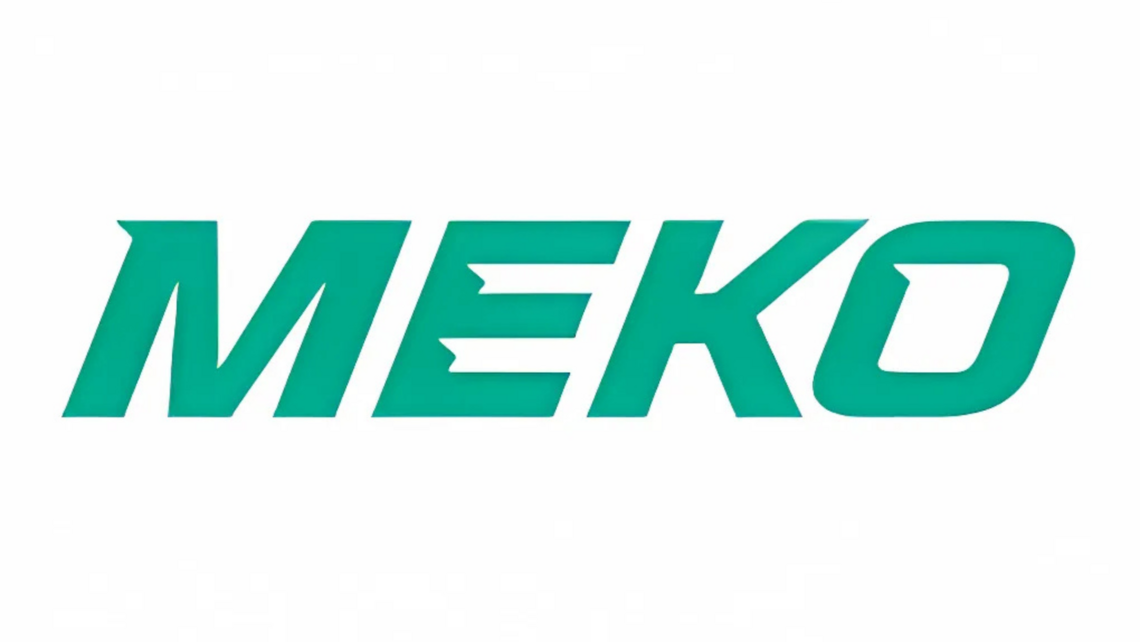
Industrial
MEKO Enhances Logistics Through Automation
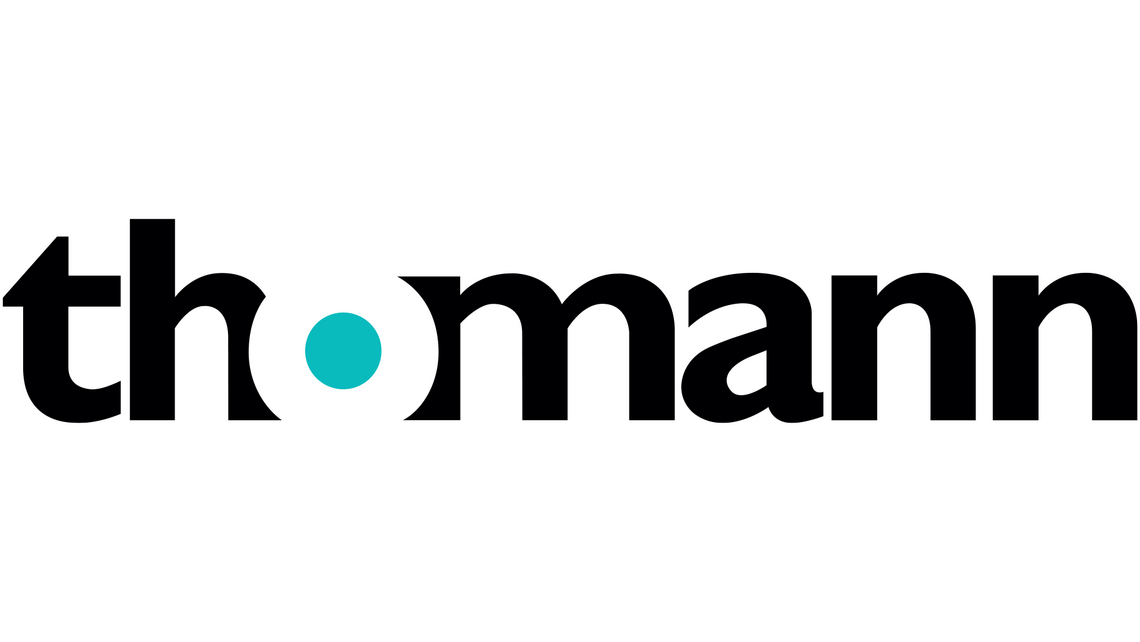
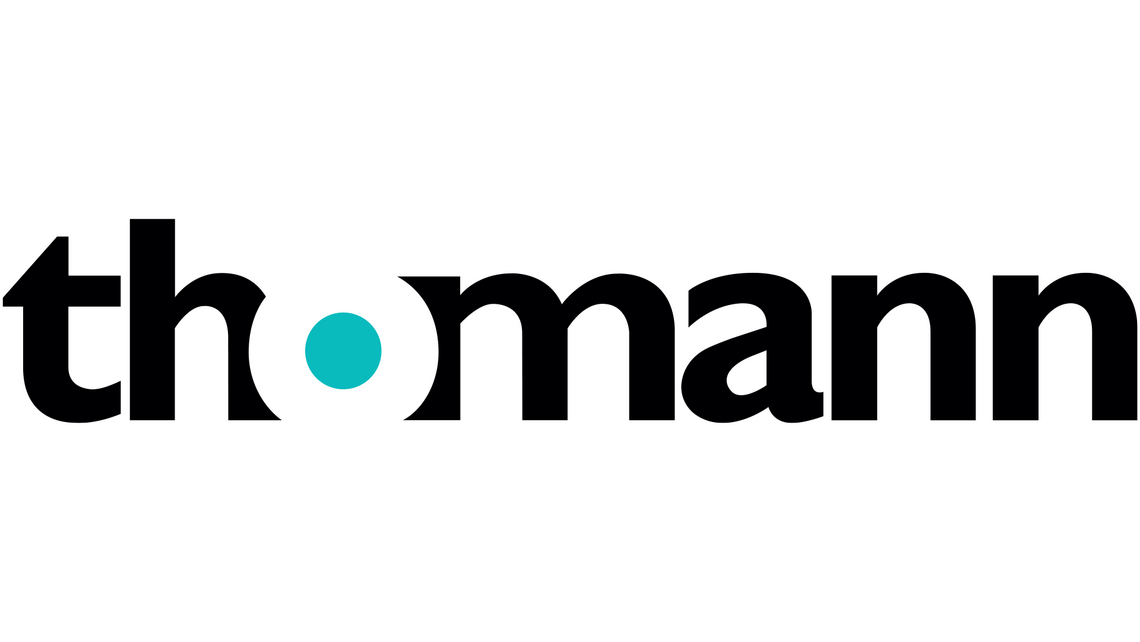
Consumer Goods
50% Faster Fulfillment for Musikhaus Thomann
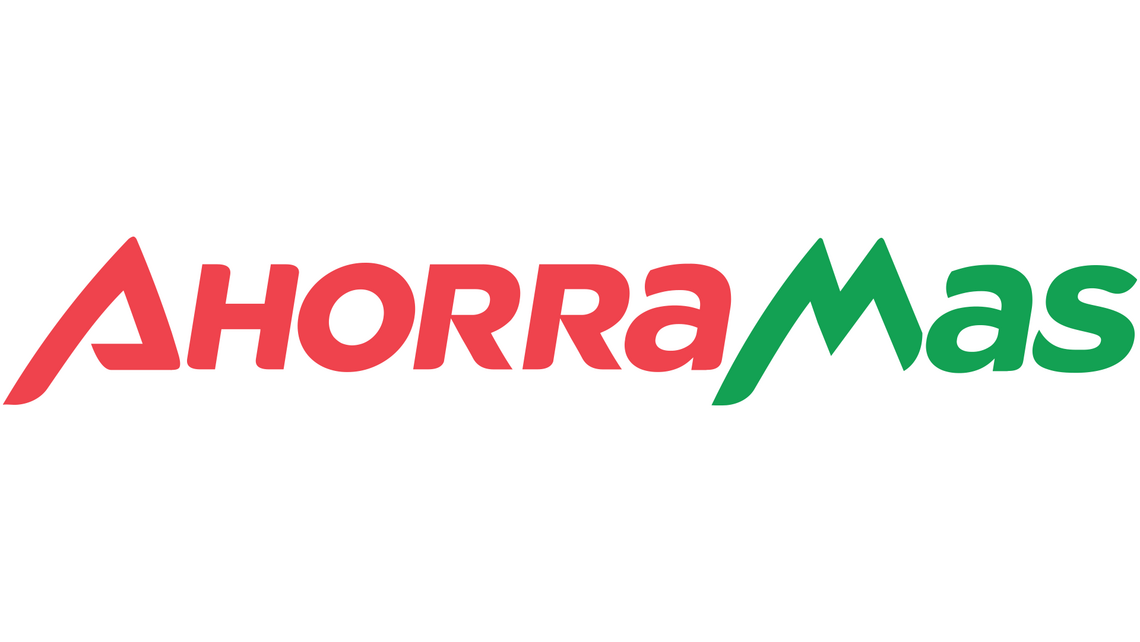
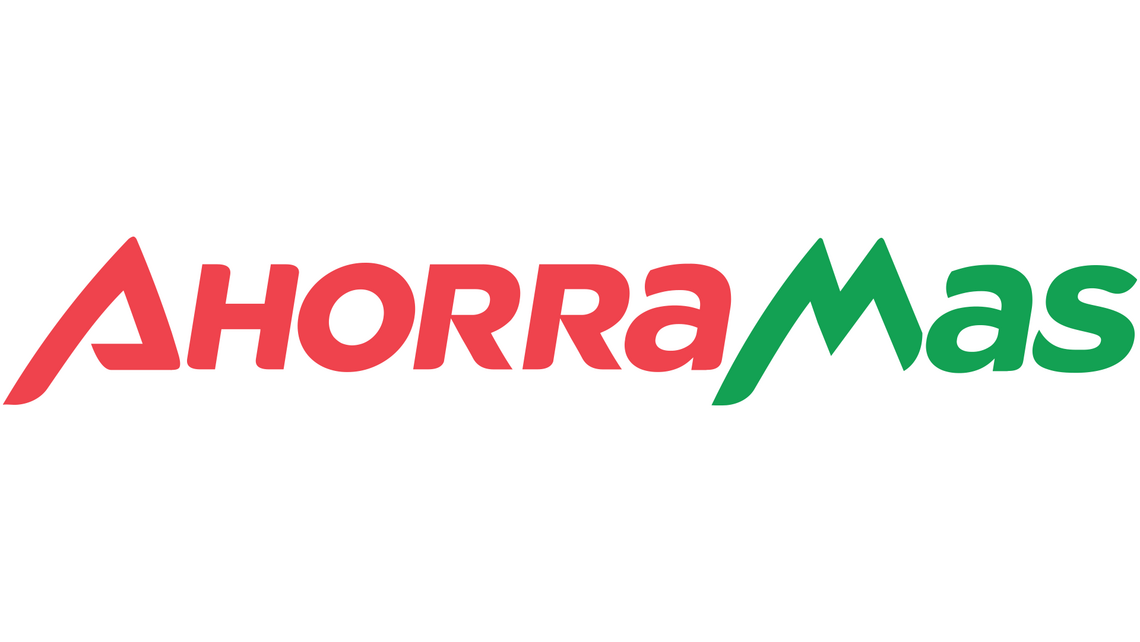
Grocery
Grocery Retail
It’s Possible: Revolutionizing Grocery Logistics for Ahorramas
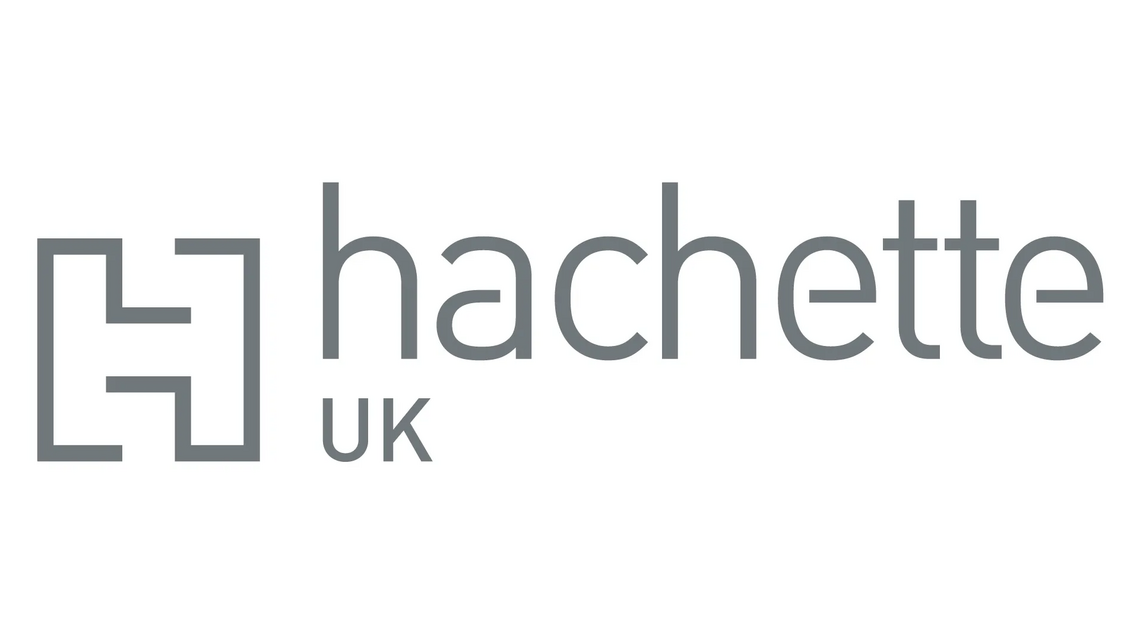
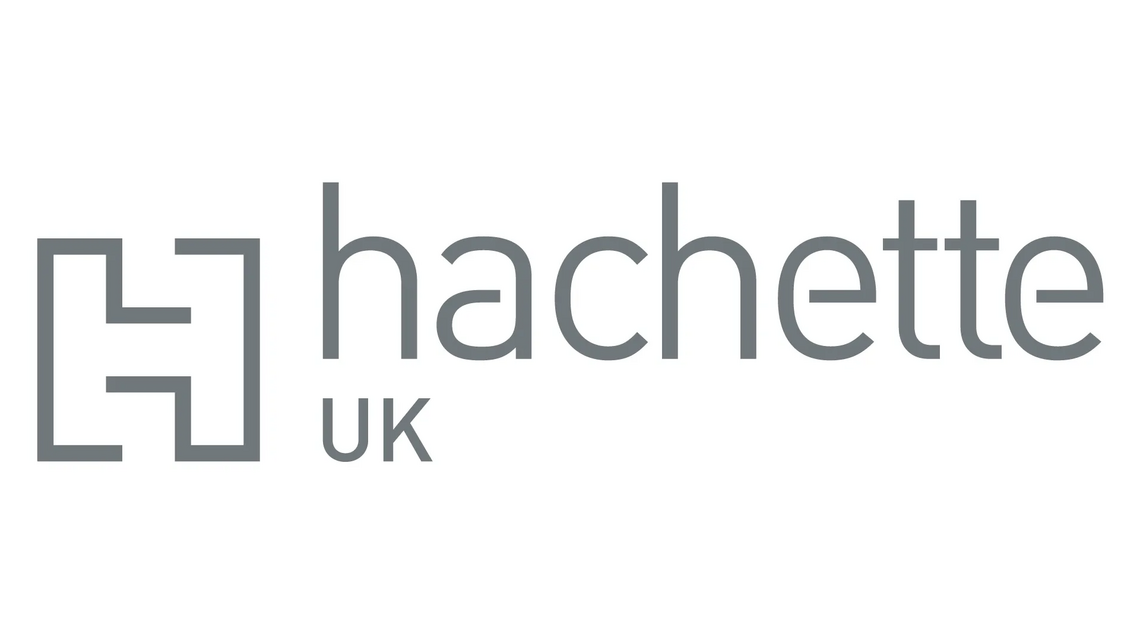
Consumer Goods
Efficiency and Flexibility made possible for Hachette UK
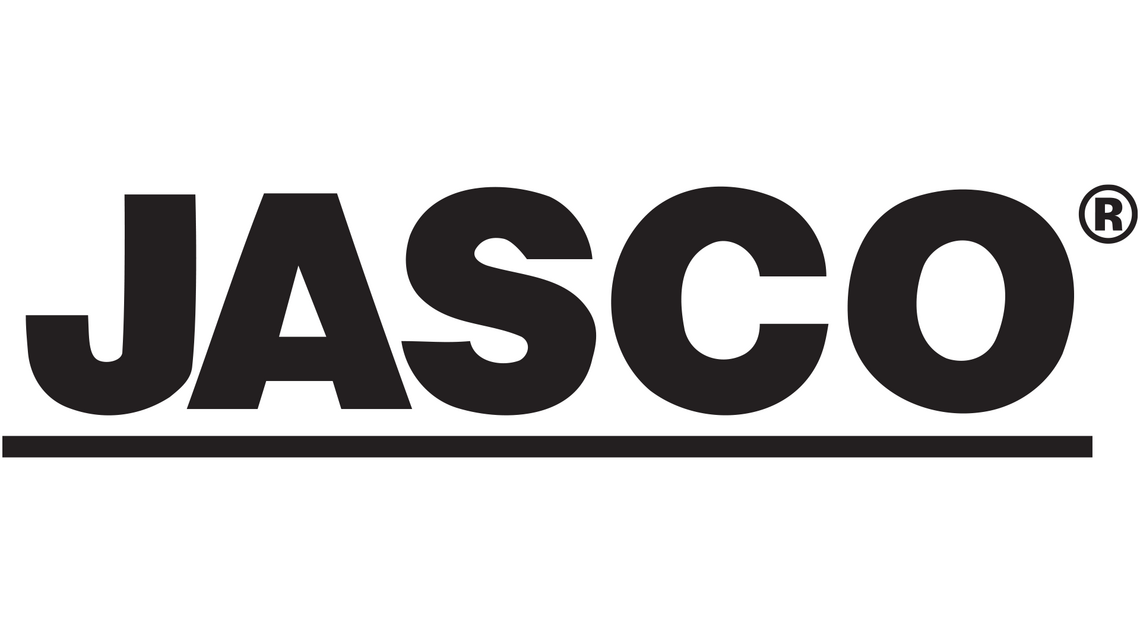
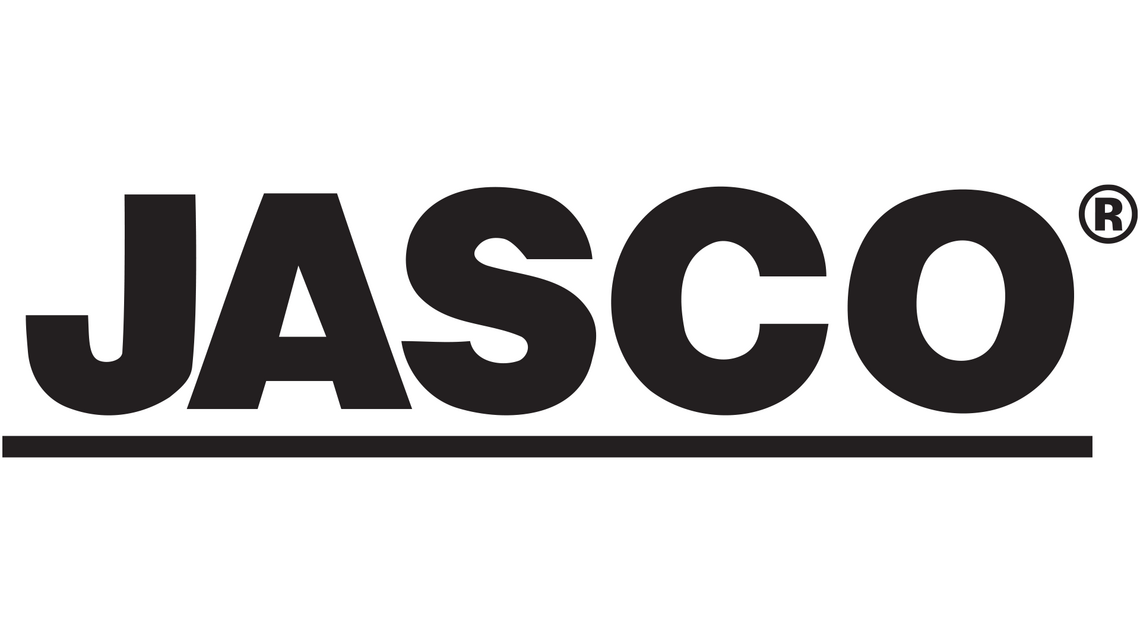
Consumer Goods
Improved Order Accuracy and Speed for Jasco
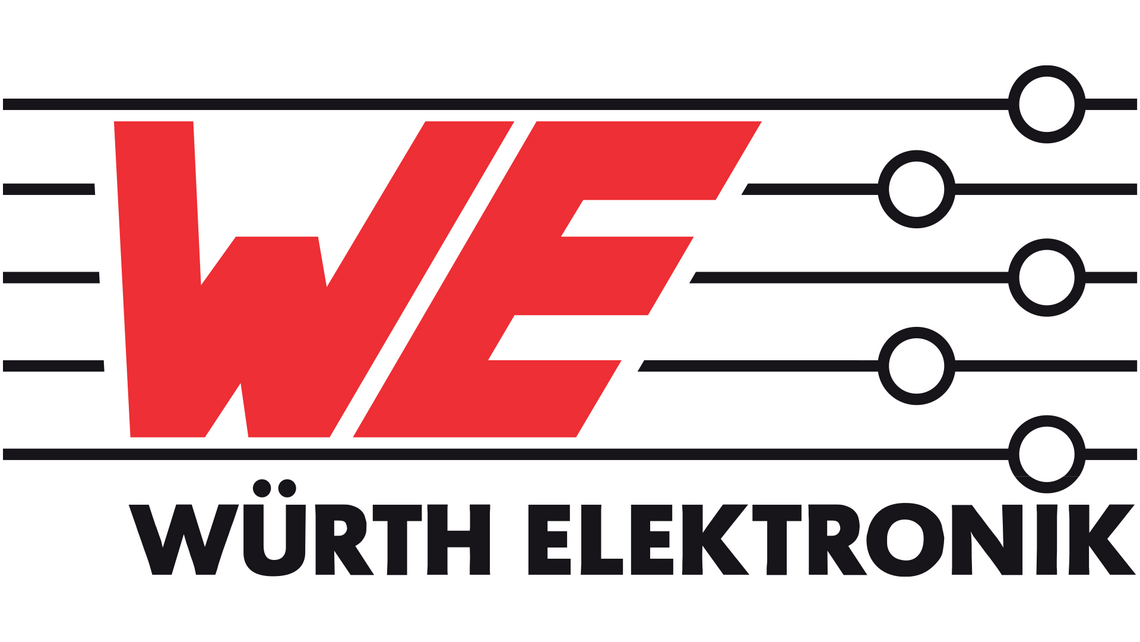
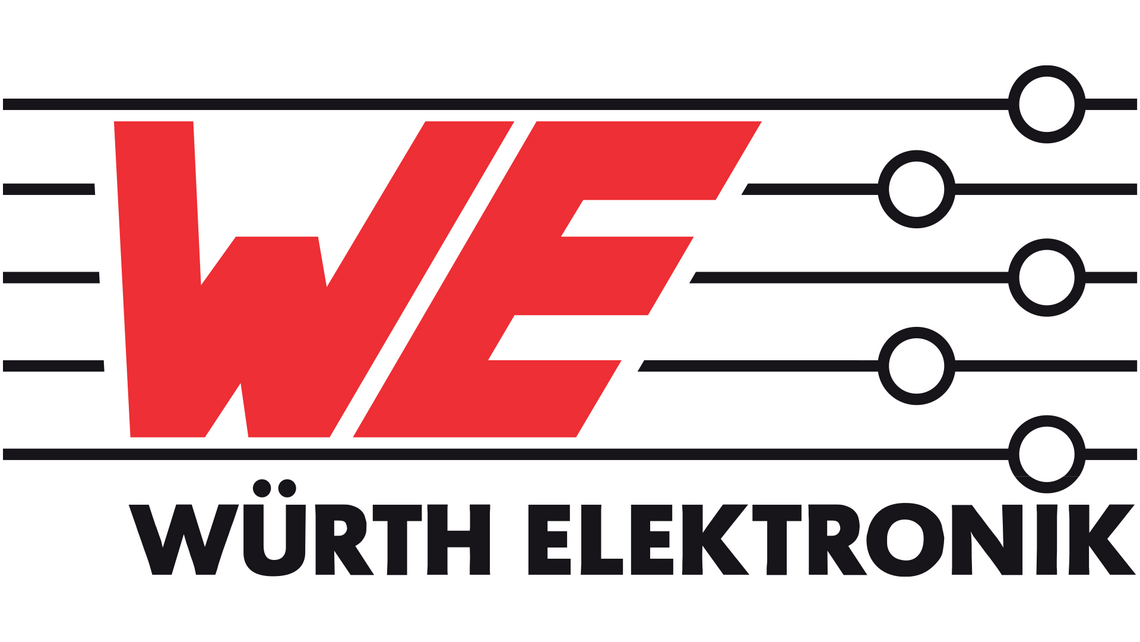
Consumer Goods
Fulfillment Scalability for Würth Elektronic eiSos
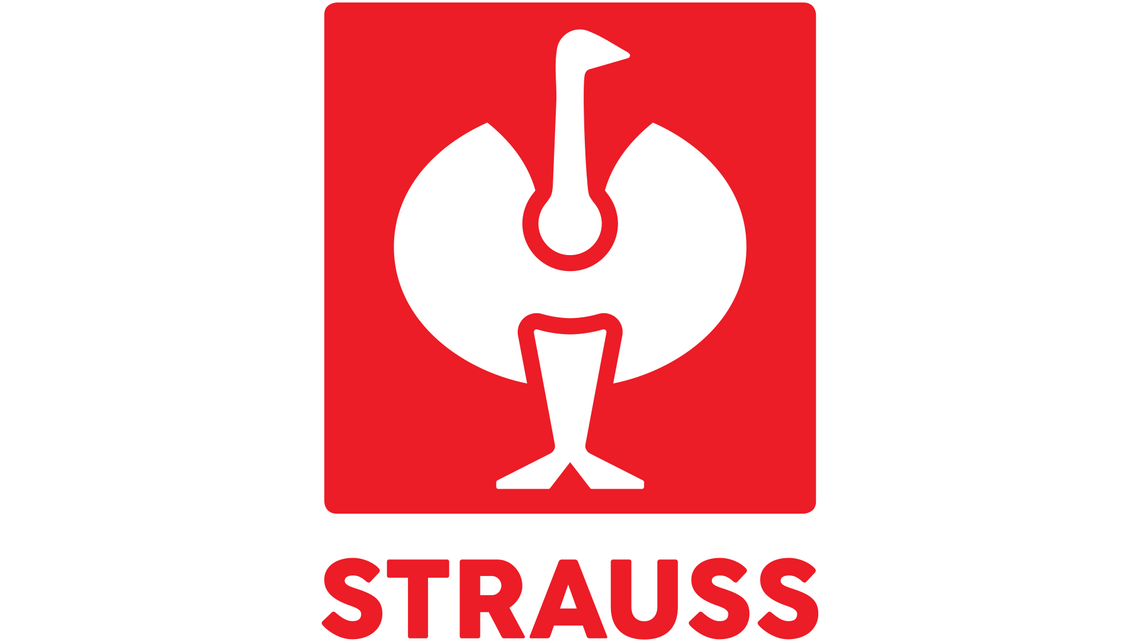
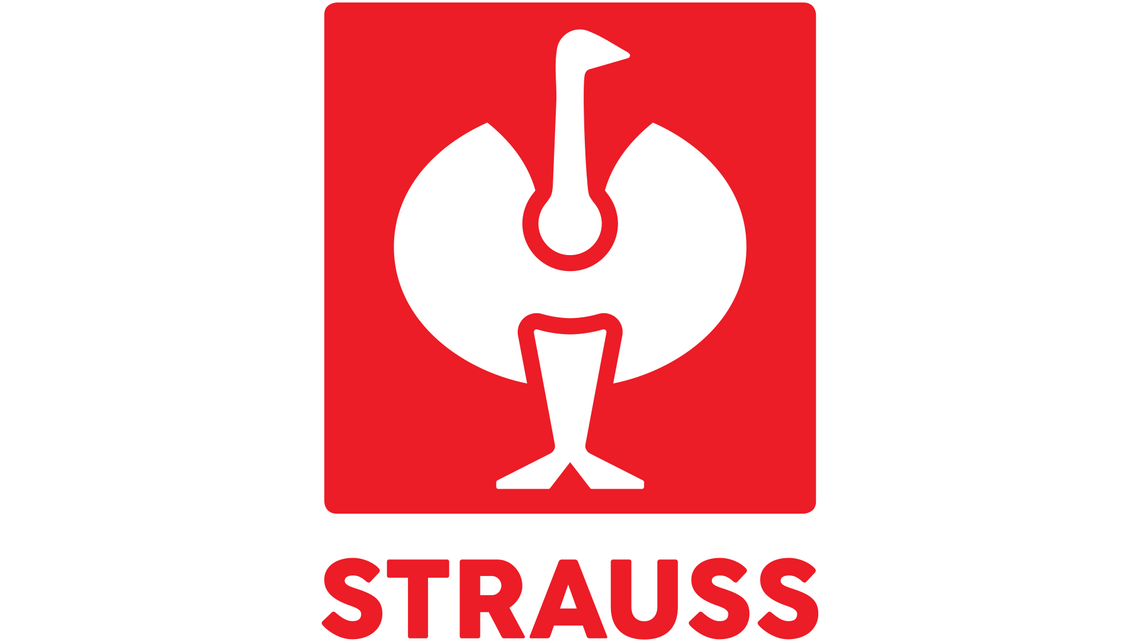
Fashion & Apparel
Engelbert Strauss Elevates Omni Channel Logistics with TGW Logistics
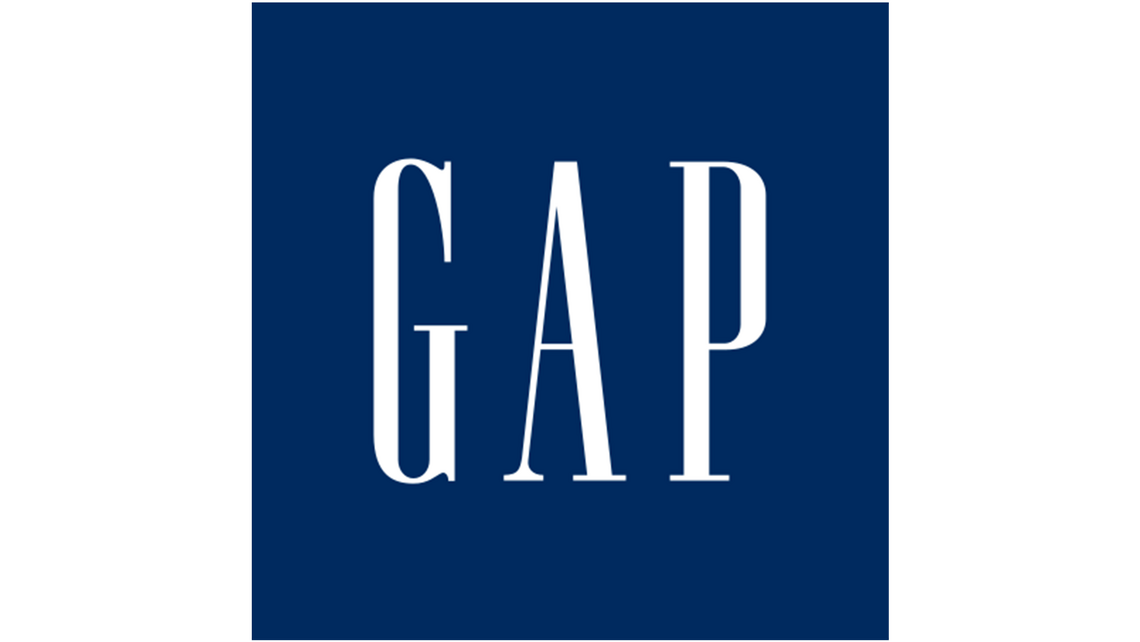
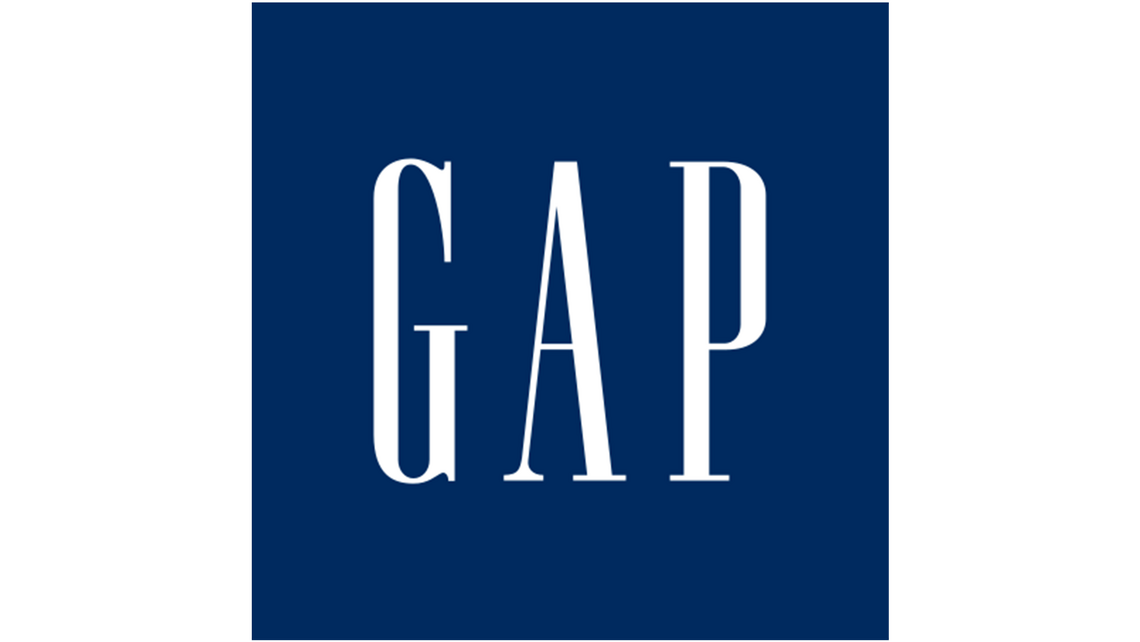
Fashion & Apparel
Gap Inc. Hits New Performance Levels with TGW Logistics
TGW Logistics is a foundation-owned company headquartered in Austria and a global leader in warehouse automation and warehouse logistics. As a trusted systems integrator with more than 50 years of experience, we deliver end-to-end services: designing, implementing, and maintaining fulfillment centers powered by mechatronics, robotics, and advanced software solutions. With over 4,500 employees spanning Europe, Asia, and North America, we combine expertise, innovation, and a customer-centric dedication to help keep your business growing. With TGW Logistics, it's possible to transform your warehouse logistics into a competitive advantage.